Air coolers are a staple in many homes and offices, offering an affordable and energy-efficient way to stay cool during hot months. But what goes on behind the scenes in the air cooler manufacturing process? From raw materials to the final product, there’s a lot of work that goes into creating these cooling machines. This guide breaks down each step, giving you a closer look at how air coolers are made in a factory.
Introduction to Air Cooler Manufacturing
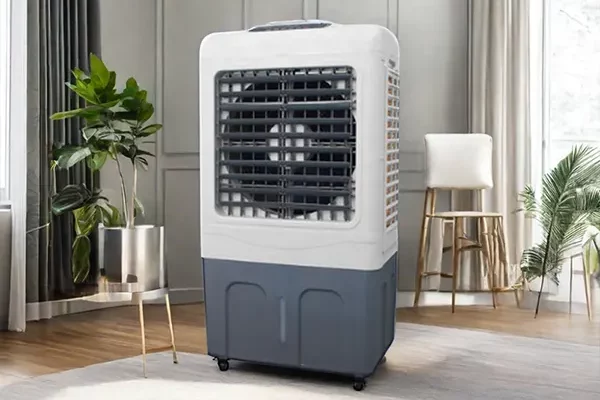
Air coolers aren’t just a simple mix of a fan and water. There’s much more to their design, and the manufacturing process is crucial in determining how well they perform. Ob es so ist a household air cooler or a commercial air cooler, each product undergoes a detailed manufacturing process in an air cooler factory. The components must fit together perfectly for maximum efficiency, and the quality control measures ensure that only the best products make it to consumers.
Raw Materials and Components for Air Coolers
Key Materials Required for Manufacturing
Every air cooler is built on a foundation of essential components, each playing a key role in ensuring efficiency and durability. Der air cooler parts list typically includes:
- Frame: Usually made from steel or plastic, offering a durable yet lightweight structure.
- Kühlkissen: Often crafted from cellulose, these highly absorbent materials are critical for absorbing water and cooling the air through evaporation.
- Motor and Fan System: A robust system designed to efficiently circulate the cooled air throughout the room.
- Water Pump: Ensures continuous circulation of water to keep the cooling pads moist.
- Electrical System: Powers the motor, Lüfter, and water pump, controlling the overall functionality of the unit.
- Water Tubing: Distributes water from the reservoir to the cooling pads.
- Control Panel: Provides user control over settings like fan speed and water flow.
Sourcing Quality Components
The success of air cooler manufacturing heavily depends on sourcing top-quality components. Performance is directly influenced by the materials used in each part, and low-quality air cooler components can lead to inefficiency or even product failure. For instance, a subpar motor or faulty cooling pads can undermine the cooler’s effectiveness. To ensure a high-performance product, a reliable air cooler factory partners with trusted suppliers for every component, meeting both industry standards and customer expectations.
Schritt 1: Design and Prototyping
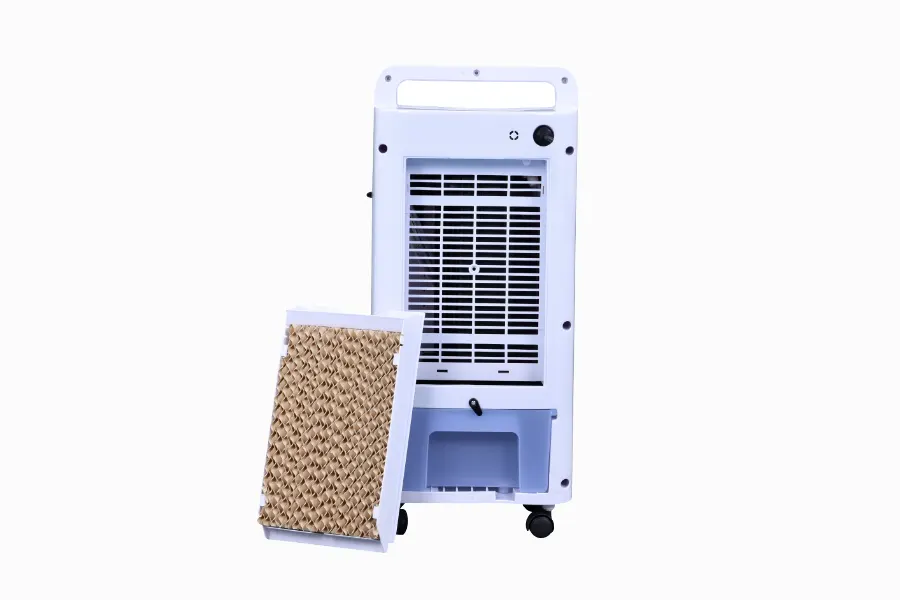
Before any parts are made, the design team works on creating the blueprint for the air cooler. This is where the look, feel, and performance factors are decided. CAD (computer-aided design) software plays a big role here, allowing engineers to create detailed and precise designs. Once the design is ready, a prototype is built to test how the air cooler performs in real-world conditions. If issues arise, adjustments are made to the design, ensuring the final product meets quality standards.
Schritt 2: Fabrication of the Air Cooler Frame
The next step in the air cooler manufacturing process is building the frame. The frame is what holds all the components together and gives the cooler its shape. It can be made from steel or durable plastic, depending on the cooler’s design. Once the material is chosen, the frame is cut, shaped, and welded (if needed) to create the basic structure. This step is crucial because the frame must be sturdy enough to withstand daily use while being light enough for easy transport.
Schritt 3: Manufacturing the Cooling Pads
Cooling pads are what make air coolers unique. These pads are designed to absorb and retain water while allowing air to pass through, cooling it down in the process. Typically, air cooler cooling pads are made from cellulose material, which is both absorbent and efficient at transferring heat. In the factory, the pads are cut to size and then treated to enhance their cooling properties. Testing comes next, as manufacturers need to ensure that each pad can absorb water effectively and maintain airflow without clogging.
Schritt 4: Motor and Fan Assembly
The motor and fan assembly is one of the most important steps in the cooler manufacturing process. The motor drives the fan, which pushes the air through the cooling pads. The motor must be strong enough to circulate air across large areas, but not so powerful that it becomes noisy or inefficient. During assembly, the motor and fan are carefully mounted within the frame, with attention paid to alignment and securing the components in place.
Schritt 5: Electrical System Integration
The electrical system powers the fan, pump, and other components of the air cooler. Wiring must be done with precision, ensuring that there’s no risk of short-circuits or electrical failure. A well-designed control panel is installed, often with settings for fan speed and water flow. Once the electrical system is integrated, it’s time to test each function to ensure that everything is working as it should.
Schritt 6: Installation of Water Pump and Distribution System
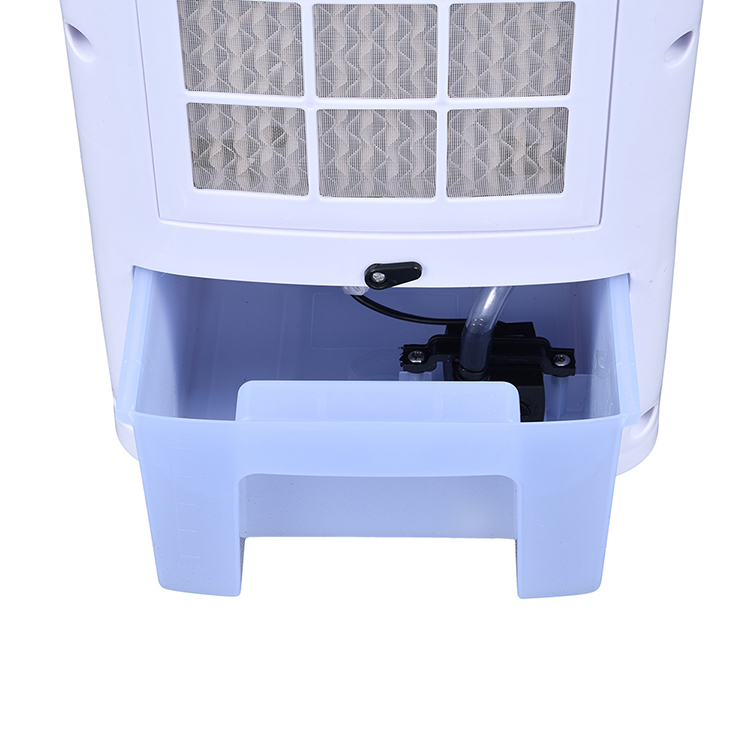
For the air cooler to cool effectively, it needs a consistent water flow to keep the cooling pads wet. A water pump is installed to circulate water from a reservoir through a system of tubes to the cooling pads. The water must be distributed evenly to ensure maximum cooling efficiency. The pump must be tested for performance to ensure there are no leaks and that water flows smoothly through the system.
Schritt 7: Final Assembly and Enclosure
With the internal components in place, it’s time to put everything together. The motor, Lüfter, cooling pads, electrical system, and water pump are all carefully assembled into the frame. Once assembled, the final enclosure or outer shell is added. This is typically made of durable plastic or metal and is designed to protect the internal components while providing an attractive finish. The unit is then sealed to prevent any dust or moisture from entering the machinery.
Schritt 8: Quality Control and Testing
Quality control is an essential part of the acooler manufacturing process. Before any air cooler leaves the factory, it undergoes rigorous testing. Engineers check the fan’s performance, ensuring it moves air effectively. They also test the water pump, the cooling pads, and the electrical system to ensure everything works smoothly. Performance tests are carried out under different conditions, and the air cooler is checked for safety and durability.
Schritt 9: Packaging and Distribution
Once the air coolers pass their tests, they are carefully packaged for distribution. Packaging is done in a way that ensures the cooler is protected during transport, preventing damage to the frame or internal components. The finished product is then ready to be shipped to retailers or directly to customers.
Trends in Air Cooler Manufacturing
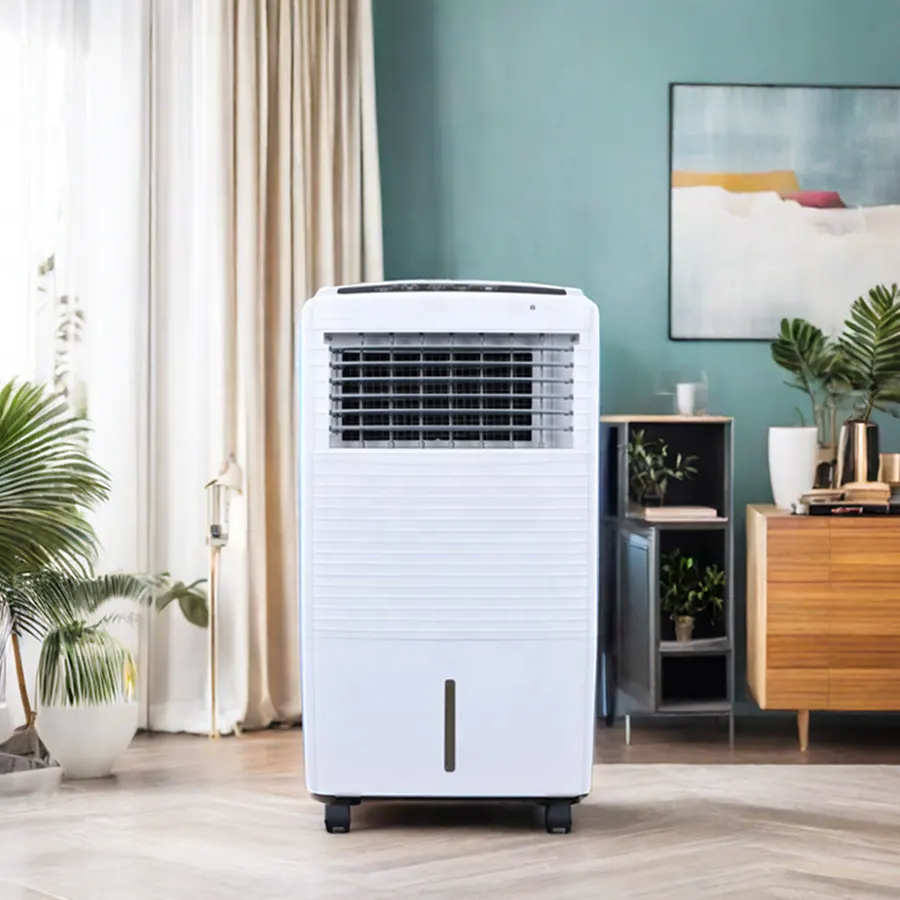
Energy Efficiency and Sustainability
As consumers become more eco-conscious, the demand for energy-efficient air coolers is growing. Modern air cooler designs focus on reducing energy consumption while maintaining performance. These coolers are often made with recyclable materials and feature energy-saving technologies that align with global sustainability trends.
Smart Features in Modern Air Coolers
Many new air cooler models come equipped with smart features, such as remote control access, Timer, and even sensors that adjust the cooling based on room temperature. These innovations not only enhance convenience but also improve energy efficiency and user experience.
Future of Air Cooler Manufacturing
The future of air cooler manufacturing is all about innovation. Manufacturers are exploring ways to integrate renewable energy sources, such as solar power, into their designs. Zusätzlich, cooler parts like cooling pads and fans are being enhanced with new materials and technology to boost efficiency and reduce costs.
Abschluss
The air cooler manufacturing process is a carefully orchestrated series of steps that requires attention to detail and precision. From selecting the right materials to final testing, each stage ensures the air cooler functions effectively and efficiently. As trends in energy efficiency and smart features continue to shape the industry, we can expect even more innovation in the years to come.
FAQs
1. What are the key materials used in air cooler manufacturing?
The main materials include steel or plastic for the frame, cellulose for the cooling pads, and durable components for the motor, Lüfter, and electrical system.
2. How long does the air cooler manufacturing process take?
The entire process can take several weeks, depending on the complexity of the cooler and the factory’s production capabilities.
3. What are the main challenges in air cooler manufacturing?
Challenges include sourcing high-quality components, ensuring the efficient integration of parts, and maintaining consistent quality control throughout production.
4. Are air coolers more energy-efficient than air conditioners?
Ja, air coolers are generally more energy-efficient than air conditioners because they use water evaporation to cool the air rather than refrigerants.
5. What trends are shaping the future of air cooler manufacturing?
Trends include a focus on energy efficiency, smart features like remote control and temperature sensors, and the use of sustainable materials in production.